Исходная ситуация
Крупная оптово-розничная компания федерального уровня столкнулась с ростом потерь при сезонном увеличении товарооборота со склада. Оптовые клиенты жаловались на задержки с получением своих заказов, на участившиеся случаи недовоза отдельных грузовых мест либо потерь сопроводительных документов. При этом оптовики имели приоритет по сравнению с отгрузками товара в собственные магазины компании, ситуация с которыми была еще хуже.
После завершения сезона отгрузки сократились, но аналогичного сокращения потерь не произошло. Менеджмент компании решил организовать и провести ряд мероприятий для наведения порядка. Было решено для начала ограничить изменения участком экспедиции (зона склада, куда поступали собранные заказы внешних и внутренних клиентов, и где они хранились в ожидании доставки), где как раз был назначен новый руководитель.
Реализация изменений не должна была даже временно ухудшить показатели работы участка экспедиции, поскольку процесс, по оценкам руководства, находился в критическом состоянии.
Наблюдение за процессом
Во многих случаях товар хранился беспорядочно, коробки повреждались, что увеличивало риск потери товарного вида. Из-за несоблюдения схемы расстановки товар вывозился на погрузочную площадку, над которой не было навеса. Груз попадал под снег и дождь, что, опять же, многократно увеличивало вероятность брака.
Стало ясным, что для сокращения потерь предстоит доработать существующие стандарты, дополнив их визуализацией, а также обучить сотрудников применению стандартов. Напомню, что стандарт, в терминах бережливого производства (kaizen), это сегодняшний наилучший способ выполнить работу. Ключевые слова здесь: 1) наилучший, 2) сегодняшний. Если завтра мы найдем способ того, как выполнить работу еще лучше, стандарт должен быть изменен, иначе он перестанет быть наилучшим.
Первые же случаи наблюдения за процессом выявили большое количество потерь времени на этапах расстановки поступивших заказов по направлениям развоза из-за бесполезных перемещений. На участке экспедиции стояли стеллажи палетного хранения, но товар постоянно ставили в проходах, потому что так «было проще». Кроме того, на участке был всего один электрический подъемник, позволяющий работать с товаром, хранящемся на верхних ярусах. В итоге товар забивал проходы, и для того, чтобы вывезти товар с мест хранения, приходилось выполнять сразу несколько операций:
- вывезти несколько поддонов с товаром из прохода;
- выполнить отбор нужного товара с мест хранения;
- вывести отобранный товар на место комплектации груза для погрузки в автомашину;
- вновь вернуть поддоны с товаром в проход, потому что других мест временного хранения под них не было.
Постоянно нарушалась существующая схема размещения товара, что приводило к потерям времени на поиск заказов и потерям товара внутри участка. Ненайденные заказы исключались из документов на поставку и позднее списывались за счет переменной составляющей заработной платы сотрудников экспедиции.
После составления схемы процесса движения цифры показали, что соотношение продолжительности действий, добавляющих стоимость, к общему времени процесса составило не более 1:6. Товар перемещался несколько раз.
РЕЗУЛЬТАТ АНАЛИЗА ПРОЦЕССА ДВИЖЕНИЯ ТОВАРА В ЭКСПЕДИЦИИ
Категория действий |
Количество
этапов |
Время, мин. |
Расстояние, м. |
Действия, добавляющие стоимость |
2 |
180 |
30 |
Перемещение |
7 |
23 |
110 |
Контроль |
3 |
45 |
|
Простой |
1 |
120 |
|
Хранение |
1 |
720 |
|
Всего |
14 |
1088 |
140 |
Предпринимались попытки получить идеи по улучшению от рабочих – исполнителей процесса, но особого энтузиазма замечено не было. По словам одного из рабочих, «здесь был и будет бардак»… Тем не менее, несколько предложений все же удалось собрать и рассмотреть.
Сбор и оценка предложений
В ходе регулярных встреч группы постепенно вырисовался план изменений, заключавшийся в следующем:
1. Изменить схему расстановки товара, привести ее в соответствие объемам и кратности отгрузок. Существующая схема разрабатывалась давно и уже не соответствовала рыночной ситуации. За это время добавились новые маршруты, новые оптовые клиенты и собственные магазины, изменились периодичность и объемы доставки по разным направлениям.
2. Установить информационные доски для рабочих участка экспедиции со следующим содержанием:
- Технология комплектации груза;
- Планировка участка с указанием правил размещения заказов;
- Примеры правильного и неправильного размещения товара;
- Примеры правильного и неправильного формирования палет;
- Количественные результаты работы участка в целом и по отдельным сотрудникам;
- Статистика по поступившим претензиям.
При изменении схемы расстановки использовались следующие принципы:
- Чем чаще уходит товар, тем ближе к проходу он ставится;
- Первый, второй (и третий) ярусы одного адреса не могут относиться к разным городам;
- Нахождение товара на улице без навеса допустимо только непосредственно перед погрузкой в машину.
Внедрение
Для внедрения изменений планировки участка были выбраны рождественские каникулы, совпавшие с инвентаризацией на складе. Сборка заказов для клиентов прекратилась, на участке остался минимум товара, который не успели доставить перед Новым годом. По иронии судьбы, именно в этот день ударил тридцатиградусный мороз, поэтому смогли поменять только адресацию внутри помещения склада. Адресацию части стеллажей, находившихся на улице, сделали лишь через несколько дней, когда потеплело. Хочется отметить, что в процессе изменения адресов хранения рабочие стали включаться в процесс и делать предложения, люди увидели, что что-то начало меняться. Были разработаны простые визуальные инструкции по работе комплектовщиков, содержащие основные действия и возможные проблемы.
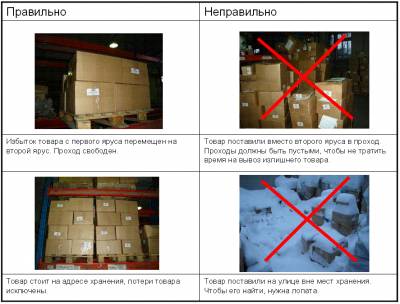
Были установлены две информационные доски размером 90 см на 180 см каждая. На одной (при входе товара на участок) разместили схему планировки, сложные случаи при расстановке, а также график выхода машин по городам. Эта доска должна помогать сотруднику правильно поставить товар на адрес хранения. На второй доске поместили дополнительную информацию (правила расстановки, показатели выработки, показатели по отдельным сотрудникам и т.п.), используемую не каждый день. Новую информацию для привлечения внимания помечали желтым клейким листочком «Новое!».
Для сокращения потерь при обмене информацией была внедрена одностраничная форма передачи смен, под которой также выделили участок информационной доски. Бригадиры смен указывали в этой форме номера проблемных заказов, сложности, возникшие с оборудованием и т.п., соответственно, другая смена вовремя получала эту информацию и успевала на нее реагировать. Кроме того, это облегчило поддержание порядка и соблюдение технологии, поскольку после подписания все ошибки размещения товара устраняла уже принимающая смена.
Не обошлось и без неудач. Так, уже после внедрения изменений технологии было предложено упорядочить и входящий на участок товар. Он поступал вперемешку, вне зависимости от направления последующей доставки, следствием чего являлся «пробег» рабочего туда-сюда между стеллажами для его расстановки. Были предприняты попытки сразу делить товар на входе по направлениям. К сожалению, это привело к тому, что товар из-за несинхронности сборки начал застаиваться перед входом на участок экспедиции, переполняя и без того небольшую площадь,. После двух дней безуспешных попыток было принято решение взять в отношении этого изменения паузу в несколько месяцев до момента планируемого изменения топологии склада.
Итог
Уже можно сказать, что ситуация принципиально изменилась. Один раз в неделю (в случайное время) проводится аудит применения технологии, контролируется нахождение товара на местах хранения (а не в проходах или без соответствия адресам), изменение количества проблемного товара, случаи неиспользуемой или противоречивой навигации и т.п. Показатели достаточно неплохие, ошибки случаются, но носят единичный характер, а это означает, что персонал принял технологию и следует ей. Количество претензий от клиентов сократилось в три раза. На участке стали регулярно наводить порядок, убирать мусор.
Особенно радует, что рабочие начали совершенствовать технологию самостоятельно. Однажды, придя проводить очередной аудит, было обнаружено, что ряд адресов содержит приписки и исправления маркером. Сфотографировав «поправки» и быстро обсудив их целесообразность с экспертной группой, адресация была изменена, и стихийные предложения стали стандартом уже в этот же день.
|